Логистика в металлургических компаниях строится особым образом.
Конечно, единого решения для всех быть не может – слишком специфичны
и отрасль, и каждое принадлежащее ей предприятие. Тем не менее принципы
построения системы существуют и здесь. Так как же решить проблемы,
не прибегая к «металлу» в голосе?
Снижение удельных издержек и повышение качества продукции в условиях
современного металлургического предприятия требуют не только внедрения
новых технологий по производству металла и проката. Не менее важно
уделять внимание управлению перемещениями сырья, топлива, полуфабрикатов,
готовой продукции, отходов и брака между производственными циклами.
Судя по опыту ведущих металлургических компаний России, при усложнении
производственной программы и введении в строй новых мощностей практически
всегда возникает проблема адекватного логистического обеспечения.
Это связано и с изменением топологии расположения самих производственных
объектов, с увеличением номенклатуры и нестабильности материалопотока.
А также с усложнением управления ресурсами, непропорциональным ростом
ошибок и накладных расходов.
ОСОБЕННОСТИ
МЕТАЛЛУРГИЧЕСКИХ ПРЕДПРИЯТИЙ
В силу специфических особенностей металлургических производственных
процессов логистическая инфраструктура – внутризаводской транспорт
(железнодорожный и автомобильный, специальный автотранспорт для
технологических перевозок) и топология складского хозяйства – играет
важнейшую роль в производстве. Инфраструктура непосредственно влияет
и на ход выполнения производственной программы, и на себестоимость
готовой продукции (рисунок 1).
рисунок
1. Система логистики металлургического предприятия
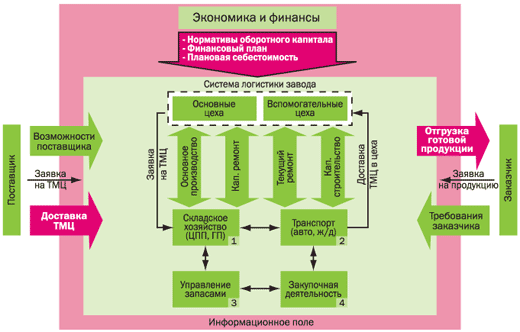
Учитывая специфические особенности (см. врезку «Внутренний мир»),
очевидно, что логистические функции играют жизненно важную роль
в сбалансированном развитии металлургического предприятия. Становясь
«узким местом», эти функции начинают сдерживать развитие производства,
аккумулируют в себе существенные издержки и негативно влияют на
своевременность отгрузки готовой продукции клиентам.
В настоящее время у металлургических заводов при увеличении объемов
производства на 20–30% в год наблюдается непропорциональный рост
затрат, связанных с логистикой, – на 40–60% за тот же период. Это
говорит о недостаточном внимании руководства компаний к развитию
логистики.
Действительно, главным считается обновление технологического оборудования
основного производственного цикла, а решению логистических задач
придается второстепенное значение. Тогда как известно: организация
производства в соответствии с логистическими принципами способна
привести к сокращению издержек на внутризаводские перемещения до
30%! Рассмотрим более подробно потенциал снижения затрат при решении
пяти ключевых проблем логистики предприятия.
ДЕЦЕНТРАЛИЗОВАННОЕ УПРАВЛЕНИЕ ВНУТРЕННИМ ТРАНСПОРТОМ
Прежде всего особого внимания к себе требует автотехника – на
предприятиях это наиболее доступный ресурс. Как правило, автотранспорт
нужен практически всем подразделениям, начиная от производственных
цехов (спецтехника) и заканчивая руководителями отделов (служебные
автомобили). Многие предприятия уже начали процесс централизации:
транспорт, приписанный к различным подразделениям завода, передается
в специализированный цех (управление). Эффект от процесса очевиден.
Вместо рассеянных по отделам ресурсов появляется централизованный
гараж и склад запчастей, сокращается общее число механиков и электриков.
Тем не менее на большинстве предприятий автотехника все еще распределяется
по подразделениям согласно предварительным заявкам на количество
единиц транспорта нужного типа и грузоподъемности. Складскому хозяйству
– для перемещения товарно-материальных ценностей (ТМЦ) в цеха и
между складами. Цехам – для технологических перевозок и самовывоза
ТМЦ со складов. Кроме этого сама автоколонна призвана решать задачи
по доставке ценностей от поставщиков на склады снабжения и доставке
готовой продукции клиентам.
Пять «углов» логистики
Основные трудности для работы службы логистики скрыты
в следующих функциональных областях металлургического
предприятия:
1) автотранспорт;
2) железнодорожный транспорт;
3) складское хозяйство;
4) управление запасами и закупками;
5) управление сбытом.
|
В итоге автотехника хоть и распределяется централизованно по подразделениям,
но насколько эффективно она используется в дальнейшем, не знает
никто. При таком подходе требуются дополнительные организационные
меры для периодического контроля результативности использования
транспорта, что, разумеется, весьма затратно и неэффективно. При
дефиците же автотехники заказчики стремятся «забронировать» за собой
побольше единиц, руководствуясь правилом: больше закажешь – больше
дадут. Тем самым еще более усугубляя и без того непростую ситуацию.
Успешный опыт других компаний показывает: потребителям транспортных
услуг лучше делать заявки на объем работы (переместить такое-то
количество ТМЦ в такие-то сроки), а не на количество техники. Только
в этом случае происходит централизация управления автотранспортом.
Что в свою очередь приносит существенный результат за счет роста
коэффициента использования, снижения холостого пробега и повышения
использования грузового объема. И что самое важное – потенциал сокращения
затрат при решении данной проблемы составляет 7–10% (от текущих
затрат на перевозки автотранспортом).
АВРАЛЬНЫЙ РЕЖИМ
РАБОТЫ Ж/Д ТРАНСПОРТА
В настоящее время свыше 85% от общего объема межцеховых перевозок
осуществляется с помощью железнодорожного транспорта. Кроме того,
внутризаводские железные дороги, работая по единому со станциями
примыкания РЖД технологическому процессу, обеспечивают металлургическое
предприятие постоянной связью с сетью государственных магистралей.
Основной задачей этого вида транспорта является наиболее быстрое
освобождение вагонов РЖД для сдачи их на станцию примыкания. При
этом важную роль играет обеспечение передвижения и погрузочно-разгрузочных
работ на соответствующих фронтах в максимально короткие сроки. Однако
сейчас на многих предприятиях железнодорожный цех работает в режиме
«пожарной команды», стараясь оперативно реагировать на постоянно
поступающие новые «вводные». Причины этого кроются и в недостаточном
планировании, и в отсутствии дисциплины работы цехов, и в скудной
информации о подходе вагонов, и в неэффективной работе с поставщиками
по обеспечению равномерности поставок вагонами.
Внутренний мир производства
Внутризаводская логистика металлургического предприятия
характеризуется следующими параметрами:
- наличием мощных потоков большого числа тяжелых грузов
(железная и марганцевая руда, лом, уголь, огнеупоры, прокат);
- большими и постоянными потоками специфических грузов
(огненно-жидкие металл и шлак, горячие слитки, агломерат);
- сравнительно менее объемным грузопотоком материально-технических
ресурсов для целей капитального или текущего ремонта и
строительства;
- достаточно большими расстояниями перевозок (средний
размер предприятий от 5 до 30 км в «поперечном сечении»
– несколько десятков и сотен километров железнодорожных
путей и автодорог);
- многообразием используемых видов транспорта (типов подвижного
состава и грузового автотранспорта);
- разбросанностью и большим количеством цехов и складов
(несколько десятков);
- наличием многочисленных и многообразных подъемно-транспортных
устройств, вспомогательного оборудования.
|
Как же снизить удельные издержки на перевозки? Выход есть: наладить
оперативную координацию действий между участниками процесса – железнодорожным
и производственными цехами, службами сбыта и снабжения. Плюс к этому
провести целенаправленную работу с поставщиками и структурами РЖД.
Разумеется, это усилия, требующие сил и средств. Но известно, что
потенциал сокращения затрат на логистику составляет 5–8% от текущих
затрат на железнодорожные перевозки.
алгоритм:
строим эффективную систему логистики
Для построения эффективной системы логистики необходимо:
1.Рассчитать показатели, характеризующие эффективность
службы логистики за определенный период времени. Разумеется,
предварительно разработав и утвердив методику расчета.
Это позволит решить две задачи: закрепить текущие показатели
до начала преобразований и, самое главное, выявить возможные
проблемы со сбором статистики и состоянием корпоративной
учетной системы. (Оборачиваемость складов, доля запасов
в оборотных активах, складские и транспортные расходы
на единицу груза, внутренний оборот вагонов и т. п.).
2.Провести комплексный аудит системы логистики завода
(см. рисунок 2 ).
3.Последовательно изучить практику работы в процессах
закупочной деятельности и транспортно-складского обеспечения,
учитывая взаимодействие с коммерческими, производственными
и финансовыми службами. В результате у вас «на руках»
будет ранжированный перечень основных проблем – потенциальных
зон прироста эффективности. Такой подход позволит выявить
наиболее существенные трудности и сосредоточить усилия
в первую очередь на их решении.
4.Спроектировать и детально проработать методы, которые
помогут справиться с проблемами именно на вашем предприятии.
|
БОЛЬШОЕ КОЛИЧЕСТВО «ПЕРЕВАЛОК»
Многим российским промышленным предприятиям производственная инфраструктура
досталась в наследство от советских времен. На лучших заводах средства
инвестировали в производство: открывались новые цеха, а транспортно-складская
инфраструктура оставалась, как правило, без изменений. И если раньше
предприятие представляло собой единый комплекс со сбалансированным
расположением подразделений относительно складов, подъездных путей
и автодорог, то ныне центры консолидации материальных потоков смещены.
Кроме этого размещение ТМЦ по складам происходит с недостаточным
анализом целесообразности – при том же объеме перемещаемых ТМЦ сейчас
мы имеем удвоенный объем транспортной работы.
рисунок
2. Комплексный подход к реформированию системы логистики промышленного
предприятия
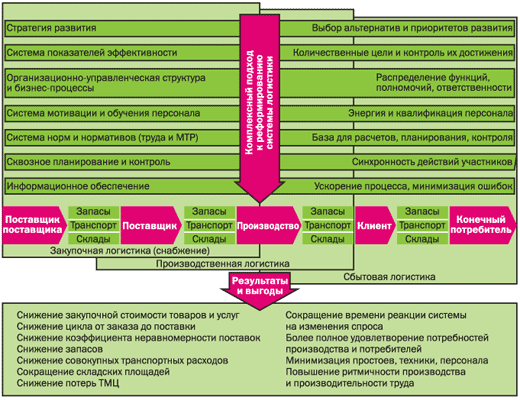
Вдобавок само складское хозяйство не отвечает современным требованиям.
На многих предприятиях происходит централизация складов, что само
по себе правильно и способствует прозрачности учета ТМЦ, уменьшению
среднего уровня запасов и сокращению возможностей для злоупотреблений.
На некоторых создается двухуровневая структура: централизованные
и кустовые склады. Что при некоторых плюсах влечет существенное
увеличение затрат на погрузочно-разгрузочные работы, а с ними неизбежно
связаны и потери ТМЦ в количественном и качественном выражении.
Помимо всего вышеперечисленного, на складах, как правило, организовано
напольное и штабельное хранение при высоте складских помещений более
6 м. В результате при значительных удельных складских издержках
– низкий коэффициент полезного использования объема.
Шире взгляд
Обратите внимание на еще одну распространенную проблему
службы логистики металлургического предприятия – узкофункциональный
подход. Если различные подразделения служб снабжения завода
работают в условиях «функциональных скважин», то каждый
отвечает за свою часть единой цепи поставок. Но за конечный
результат ответственных нет. Конечно, виновного в срыве
поставок можно найти быстро, но вопрос увеличения себестоимости
продукции из-за низкой эффективности снабжения все равно
останется открытым.
|
Обозначив проблему, можно перейти к проработке методов ее решения.
Тем более потенциал сокращения затрат, возникающих вследствие перечисленных
трудностей, составит 10–15% от текущих расходов, связанных со складским
хозяйством.
НЕЭФФЕКТИВНОЕ УПРАВЛЕНИЕ
ЗАПАСАМИ
С точки зрения управления запасами для металлургического предприятия
целесообразно выделить три основные группы ТМЦ.
1. Сырье и основные материалы (аглосырье, угли, ферросплавы,
металлолом, цветные металлы и пр.).
2. Оборудование и запчасти (технологическое, нестандартное,
а также электротехническое, сменное и др. оборудование).
3. Вспомогательные материалы (черные металлы, лесоматериалы,
ГСМ, инструменты, запчасти, химикаты, спецодежда и т. д.).
Для первой группы характерно наличие нормативной базы расхода
ТМЦ с привязкой к выходу готовой продукции. Соответственно существенных
проблем поддержания заданного уровня запасов при объемно-календарном
планировании закупок нет. Другое дело, актуальность самой нормативной
базы и уровня запасов.
Основной объем второй группы ТМЦ идет, как правило, на капитальный
или текущий ремонты технологического оборудования, а также на строительство.
Все они предполагают высокую плановость и проектное управление.
Тем не менее на некоторых предприятиях недостаток тех или иных запчастей
обнаруживается уже непосредственно при осуществлении ремонта. Причины
кроются в отсутствии прогнозирования остатков, непрозрачности учета
и просто халатном отношении к планированию. В результате резко возрастает
процент срочных закупок. Что в свою очередь неминуемо увеличивает
удельные транспортные расходы – то, что можно было доставить железнодорожным
транспортом, доставляется автомобильным. Также увеличивается закупочная
стоимость ресурсов – у поставщиков есть свой график производства,
и нарушение его влечет удорожание продукции.
Третья группа ТМЦ вместе со второй образуют 90% всех наименований
и всего лишь 20% от стоимости закупаемых ТМЦ. Приобретением товаров
этой последней группы занимается около 80% персонала, то есть именно
она «забирает» на себя львиную долю трудозатрат. Тогда как именно
в этой сфере можно и нужно применять компьютеризированные модели
управления запасами. Но, к сожалению, этого не происходит: либо
«руки не доходят», либо доработка корпоративной информационной системы
слишком дорога по сравнению с ожидаемым эффектом. В результате управление
запасами передается закупщикам, а объем закупаемых партий определяется
«на глазок» (в самых вопиющих случаях даже без учета запасов в пути
и ремонтного фонда).
Необходимо учитывать и главную задачу закупщиков – обеспечение
производства достаточным количеством сырья, материалов, а также
оборудованием и запчастями для основной деятельности и своевременного
ремонта технологической оснастки. Разумеется, закупщики – не специалисты
по управлению запасами. Они отлично знают рынок поставщиков и их
особенности, знакомы со свойствами номенклатурных позиций, разбираются
в методах выбора (будь то открытые или закрытые тендеры, конкурсы
и др.). Но они не владеют способами минимизации запасов без риска
для производства. Должны ли они при всем этом уметь еще и управлять
запасами?
Трудности перевоза
По статистике, из общего объема межцеховых
перевозок на металлургических предприятиях более 85% приходится
на железнодорожный транспорт. На данный момент наблюдаются
следующие связанные с ним проблемы:
- простои подвижного состава у цехов из-за ожидания погрузки/выгрузки;
- большое количество маневровых работ;
- неравномерная нагрузка и простои у пункта подготовки
вагонов;
- ожидание готовности таможенных документов после выставления
груженых вагонов на станцию отправления;
- неправильный учет движения вагонов по территории предприятия.
Все это приводит в конечном счете к увеличению
цикла внутреннего оборота вагонов. Либо к высоким платежам
и штрафам за пользование вагонами и за невыполнение планов
перевозок.
Тем не менее способ снизить издержки,
связанные с эксплуатацией железнодорожного транспорта, существует.
|
Конечно, это зависит от размеров предприятия и системы мотивации,
индивидуальной для каждого предприятия. Но фактом остается то, что
в настоящее время на большинстве предприятий функция управления
запасами на этапе снабжения отдана несведущим в данном вопросе сотрудникам.
А система мотивации либо отсутствует в принципе, либо далека от
совершенства. В результате закупщики, перестраховываясь либо злоупотребляя,
накапливают на складах большие объемы ТМЦ, «замораживая» оборотные
средства, столь необходимые предприятию для развития. Многие из
этих ТМЦ со временем превращаются в «неликвиды», по 2–3 года и более
невостребованные производством. Они продолжают лежать на складах,
«поедая» электроэнергию, отопление, увеличивая затраты на ежегодную
инвентаризацию и создавая почву для хищений. Тогда как посчитано:
потенциал сокращения затрат на неэффективное управление запасами
составляет 15–25% от текущих расходов на их содержание. Есть над
чем задуматься.
Рассчитайте
потенциальную выгоду
Затраты на логистику на металлургическом предприятии
в целом можно снизить, последовательно решив пять основных
задач, о которых говорится в статье. Потенциал сокращения
затрат при решении соответствующих проблем будет следующим:
1) 7–10% – децентрализованное управление внутренним
автотранспортом (обслуживание и управление, технология
и ТМЦ);
2) 5–8% – авральный режим работы железнодорожного
транспорта («сгущенный» приход, непредсказуемость цехов,
подход вагонов РЖД);
3) 10–15% – большое количество перевалок при многоуровневом
складском хозяйстве (нерациональное размещение складов
и распределение ТМЦ по складам);
4) 15–25% – неэффективное управление запасами;
5) 5–10% – ориентация на минимальную закупочную цену,
а не на общие затраты.
|
ОРИЕНТАЦИЯ
НА МИНИМАЛЬНУЮ ЗАКУПОЧНУЮ ЦЕНУ
Закупщик, ключевое лицо в системе материально-технического снабжения
металлургических предприятий, выбирая того или иного поставщика,
ориентируется в первую очередь на минимальную закупочную цену. Этот
критерий в преобладающем большинстве случаев является основным и
чуть ли не единственным (при равном качестве закупаемых ТМЦ).
На определение минимальной величины ориентированы также и тендерные
процедуры (кроме того, учитываются уровень качества, способность
поставщика выполнить заказ в нужном объеме, удаленность и др.).
Но мало на каком предприятии включаются в оценку такие критерии,
как выполнение равномерного графика поставок, удобство погрузочно-разгрузочных
работ, транспортировки и обеспечение сохранности на территории предприятия.
Тогда как именно они существенно увеличивают конечную стоимость
закупаемых партий при доставке в цеха.
В пределах отдельно взятого подразделения специалисты добросовестно
стремятся к минимизации затрат. Но без системного подхода это зачастую
приводит к росту совокупных расходов в системе снабжения. Например,
те же закупщики редко требуют от поставщиков обеспечения равномерности
поставок. В результате предприятие сталкивается с проблемой волнообразного
прихода вагонов и автотранспорта под выгрузку (на жаргоне специалистов
– «залповая поставка» или «сгущенный приход»). Ресурсы грузчиков,
складов и внутреннего транспорта либо простаивают, либо, напротив,
их не хватает. Подъездные пути заполняются вагонами, существенно
сокращая пространство для маневров. Груженые составы скапливаются
и у фронтов погрузки, так как количество первых не соответствует
мощностям последних.
Предприятие вынуждено платить за сверхнормативный простой вагонов
РЖД и внешний автотранспорт под выгрузкой. Снижаются показатели
оборачиваемости для арендованных вагонов, существенно возрастают
издержки на маневровые работы. А причина проста – отсутствие адекватной
системы планирования и координации поставок. В то время как потенциал
сокращения затрат, связанных с перечисленными проблемами, составляет
порядка 5–10% от совокупных расходов на погрузочно-разгрузочные
работы, внутренние перемещения ТМЦ и простой подвижного состава.
ПОИСК РЕШЕНИЯ
Признать наличие проблем на своем предприятии непросто. Однако
и это только полдела. Необходимо выстроить грамотную стратегию принятия
решений с тем, чтобы минимальными затратами достигнуть максимального
экономического эффекта. Для этого прежде всего необходимо понять,
к чему стремиться.
К экспертам нашей компании часто обращаются клиенты с просьбой
дать пару-тройку типовых эффективных решений, которые можно было
бы применить на собственном предприятии. От такого подхода хочется
сразу предостеречь: не существует единой схемы успешной работы системы
логистики, одинаковой для всех. Как нет единого рецепта от головной
боли для всех людей. Просто потому, что причины проблем могут быть
так же различны, как и сами предприятия, даже если они работают
в одной отрасли. Однако не стоит отчаиваться и забывать, что принципы
организации эффективной системы логистики одинаковы